WELDING
Our welder’s extensive knowledge and expertise working with these materials allow customers to achieve the highest caliber results in their products, and our machinists utilize CNC lathe and mill capabilities to ensure your products consistently meet industry standards.
UNIQUE WELDING STATION DESIGN
To increase efficiency in Pumping Solutions shop, welding gases, compressed air, and cooling water are piped to each welding station. The stations can run four argon regulators and one mixed gas regulator at a time. Pumping Solutions uses stainless steel to pipe the welding gases from the liquid source, further enhancing the quality of fabrication.
LEADING WELDING TECHNOLOGY
Pumping Solutions combines welding skills with the latest welding technology to produce industry-leading weld quality. With the latest in orbital welding equipment technology and manual TIG welding capabilities, CSI craftspeople take pride in their workmanship and ownership of every project that is worked on.
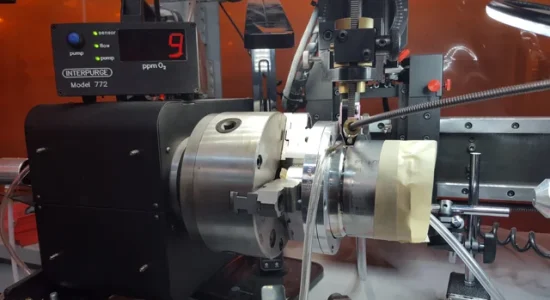
PRECISION LATHE WELDING
We utilize the latest lathe welding technology to produce precise, repeatable weld results on a wide range of circumferential parts. This machine optimizes our process and improves weld quality, all while reducing costs..
MACHINING
Machinists at Pumping Solutions ensure your products consistently meet industry standards. With our CNC lathe and mill capabilities, we are leaders in the manufacturing of fittings in sanitary stainless steels as well as AL-6XN and Hastelloy C-22.
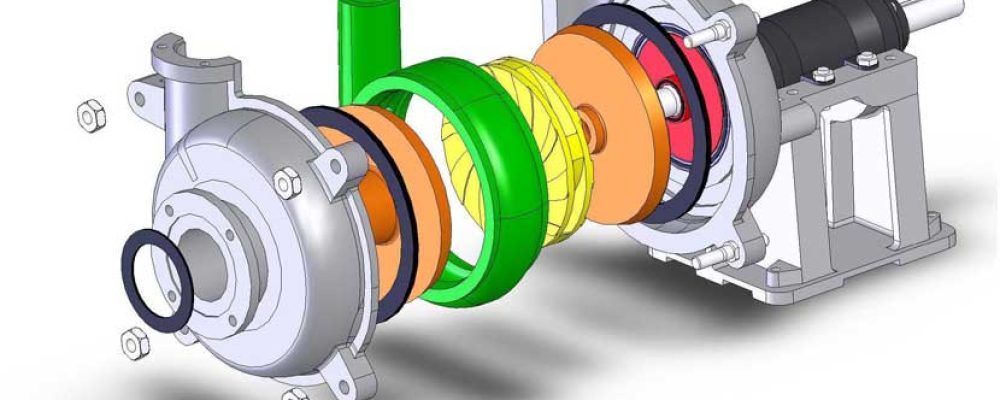
STANDARDS AND TOLERANCES
At Pumping Solutions, manufacturing methods comply with the latest industry standards. We are actively involved in the committees that write the standards for the industries we serve. As a result, we have a deep understanding of industry standards, allowing us to consistently meet the tolerance requirements for your components.
MACHINING TRANSFER PANELS
When manufacturing transfer panels, our machinists use a precision machining process to bore ports through 1/4 inch (or thicker) polished plates. This ensures tolerances meet or exceed industry standards for proper jumper fit-up and leak-free design.
CUSTOM-MACHINED FITTINGS
We like challenges at Pumping Solutions. Our experts take an “outside-the-box” approach when developing designs for custom machined components. Let us take on your next challenge.

SUPERIOR MACHINING EQUIPMENT
At Pumping Solutions, we utilize equipment to meet the needs of the sanitary processing industry.
- Computer numerically controlled (CNC) & manual lathes
- CNC & manual mills
- Auto band saw
- Finishing equipment
- Various inspection tools to verify dimensions and tolerances
FINISHING
We are precise when polishing components to provide consistent, quality surface finish results. Pumping Solutions takes a systematic approach to surface finishing, allowing us to provide consistent, high quality results on your products. Our in-house polishing capabilities allow us to meet expedited project schedules while maintaining product quality.
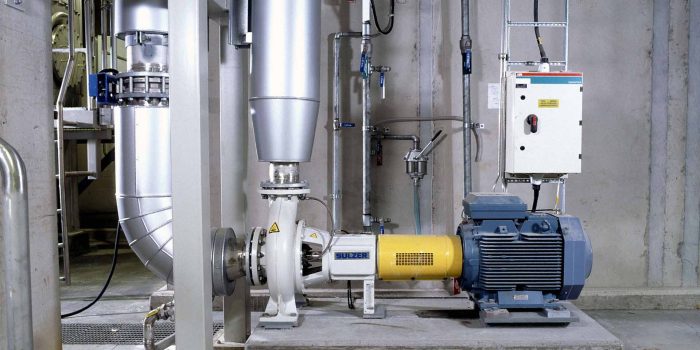
OUR EXPERIENCE WORKS FOR YOU
With over 50 years of experience in finishing components and equipment, Pumping Solutions is the leader in providing this service for the sanitary process industry. We are actively involved in organizations like 3-A and ASME BPE. Our active involvement allows us to incorporate the latest standards into our surface finishing process to meet the needs of our customers.
CLEANLINESS IN MIND
Similar to our work stations, the polishing area at Pumping Solutionsnis uniquely designed to be clean, safe, and efficient. The polishing department is in a separate area from our production area. The space has its own climate-controlled ventilation and filtration system that helps keep dust contained.
Every finished product goes through a detailed final inspection process to ensure it meets finish specifications and dimensional tolerances.
FINISHING TECHNIQUES
We make the success of your project a priority at Pumping Solutions. Our finishing experience helps us meet your quality requirements.
- Wide range of mechanical surface finishing
- Electropolish capability to less than 10 Ra (316L stainless steel)
- Glass bead blasting
- Passivation capabilities utilizing citric acid
- Ultrasonic cleaning
- Surface finish checked with a profilometer for conformity to specifications